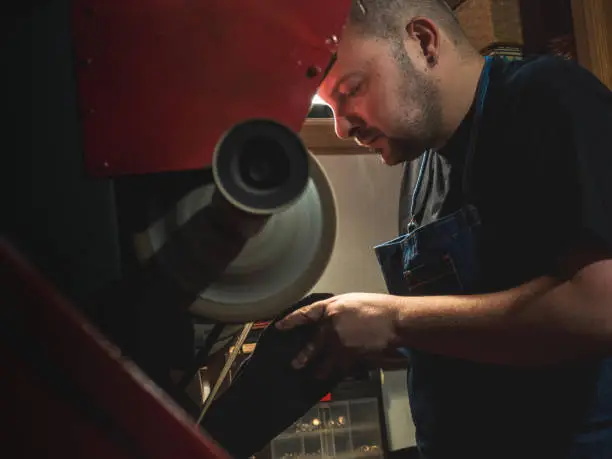
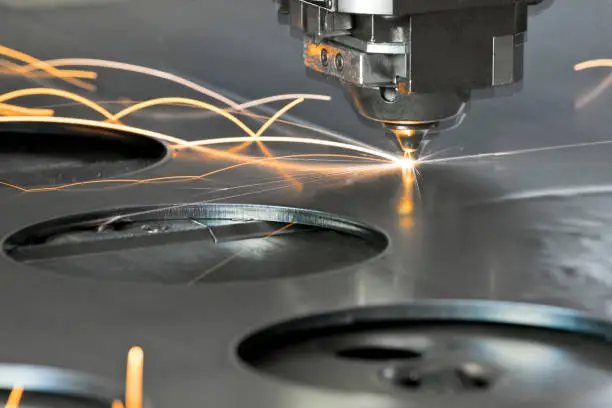
How CNC Machinery Enhances Metal Spinning: Precision, Efficiency, and Consistency in Modern Manufacturing
Metal spinning has evolved significantly over the years, transforming from a purely manual technique into a sophisticated, automated process. Today, the integration of CNC (Computer Numerical Control) technology has further revolutionised metal spinning, enhancing precision, efficiency, and consistency in the production of complex metal components. CNC metal spinning offers a highly effective solution for industries like aerospace, automotive, and medical equipment manufacturing, where accuracy and quality are paramount.
This blog explores the role of CNC machinery in metal spinning, examining how it elevates the manufacturing process and enables companies to meet the stringent demands of modern production.
Understanding CNC Metal Spinning
Metal spinning involves shaping a flat sheet or tube of metal by rotating it at high speeds on a lathe and pressing it against a mould or mandrel. Traditionally, this process was done by skilled artisans who used hand tools to shape the metal. While manual spinning still has its place, especially for bespoke or artisanal items, CNC metal spinning has become the industry standard for high-volume production.
CNC machinery automates the metal spinning process, using pre-programmed software to control the spinning lathe and tools with incredible precision. This automation produces consistent, high-quality components with complex geometries, tight tolerances, and minimal human intervention.
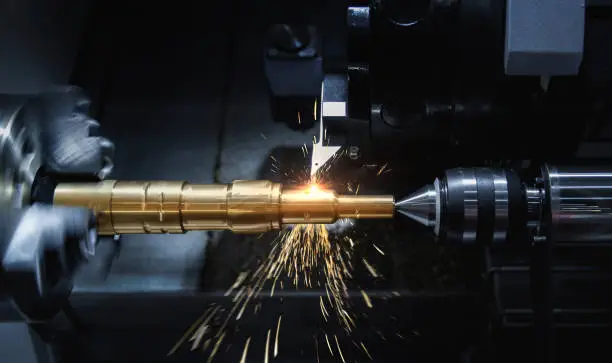
The Advantages of CNC in Metal Spinning
CNC metal spinning offers several key benefits that make it ideal for high-demand industries:
Enhanced Precision and Repeatability
CNC technology enables manufacturers to achieve exceptional precision, ensuring that each component is produced to exact specifications. The software-controlled process eliminates much of the variability inherent in manual spinning, resulting in parts with tight tolerances and high repeatability across large production runs. This level of accuracy is essential in industries where even minor deviations can affect the performance and safety of a product, such as aerospace or medical devices.
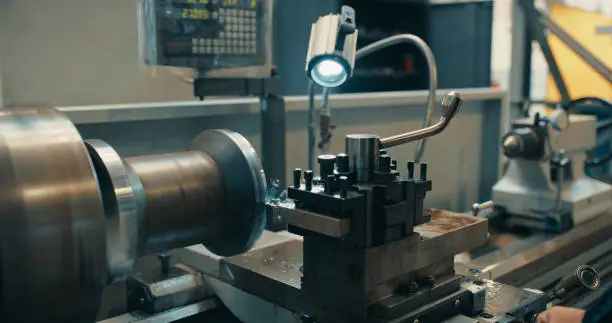
Increased Efficiency and Speed
CNC metal spinning significantly reduces production time compared to manual spinning. The automation of the process allows machines to operate continuously with minimal downtime, increasing throughput and enabling faster turnaround times. According to industry studies, CNC machines can be up to 15 times faster than manual processes, which is invaluable for manufacturers looking to meet tight production schedules.
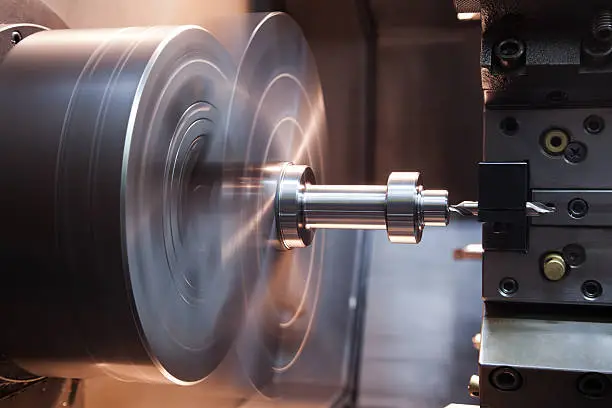
Complex Geometries and Design Flexibility
CNC machinery offers the ability to create intricate shapes and complex designs that would be challenging or even impossible to achieve manually. With the flexibility to program various shapes and adjust specifications, CNC metal spinning caters to a wide range of design requirements. This versatility supports diverse applications, from automotive components with detailed contours to medical devices requiring precise dimensional accuracy.
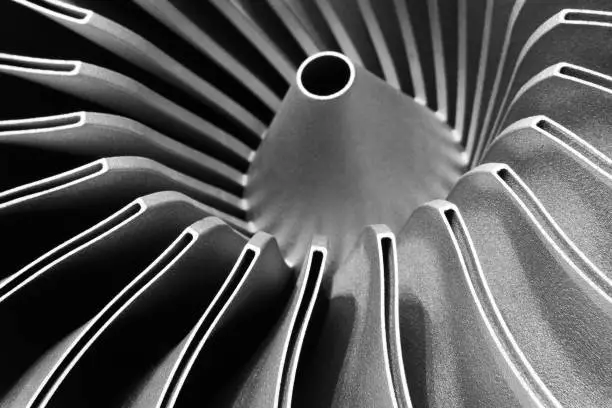
Reduced Material Waste
One of the key advantages of CNC metal spinning is its efficiency in material use. By following programmed paths, CNC machines minimise excess material removal, reducing waste and lowering costs. This precision helps manufacturers optimise material use, which is particularly beneficial when working with expensive or scarce materials like titanium or high-strength alloys.
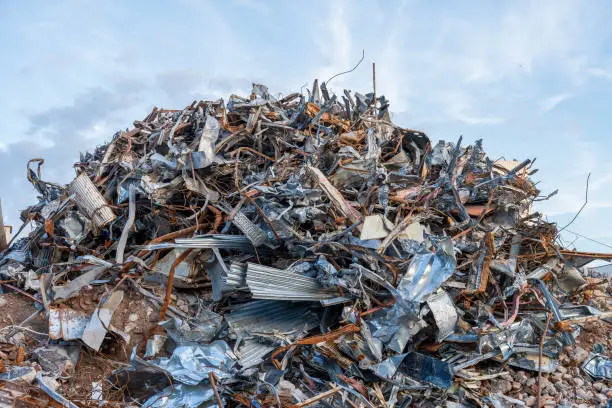
Lower Labour Costs and Enhanced Safety
CNC technology reduces the need for extensive manual labour, as one operator can oversee multiple machines simultaneously. This reduction in labour lowers production costs and enhances workplace safety by minimising direct human interaction with heavy machinery. Automation also decreases the likelihood of accidents, creating a safer environment for manufacturing staff.
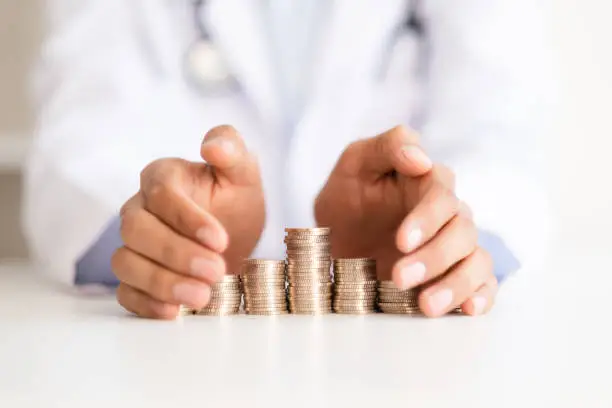
CNC Metal Spinning Techniques
CNC metal spinning involves several techniques tailored to different materials and requirements. Here are some of the most commonly used methods in CNC metal spinning:
- Conventional CNC Spinning: This primary method involves shaping a metal disc over a mandrel to create simple forms like cylinders and cones. Conventional CNC spinning is ideal for symmetrical shapes that require precise, smooth finishes.
- Shear Spinning: Shear spinning reduces the material thickness while forming, making it suitable for components requiring uniform wall thickness. This technique is commonly used in aerospace applications, where lightweight yet durable components are essential.
- Tube Spinning: Specifically designed for creating hollow, cylindrical shapes, tube spinning manipulates tubes rather than solid discs, enabling the production of seamless components for automotive and industrial uses.
These techniques highlight the adaptability of CNC metal spinning to meet various industrial requirements, supporting everything from high-strength aerospace components to decorative lighting fixtures.
Applications of CNC Metal Spinning in Industry
CNC metal spinning has broad applications across industries that require high-quality, precisely engineered components. Here are some notable examples:
- Aerospace: CNC metal spinning is widely used in the aerospace sector to produce lightweight, robust components that can withstand extreme conditions. The precision of CNC technology ensures that parts like nose cones, fuel tanks, and exhaust systems meet stringent safety and performance standards.
- Automotive: In automotive manufacturing, CNC metal spinning creates components such as wheel rims, exhaust parts, and other critical elements that require durability and exact dimensions. The speed and efficiency of CNC metal spinning make it ideal for high-volume automotive production.

- Medical Devices: CNC technology allows for producing complex, high-precision medical devices, such as surgical instruments and implants. These components often require exacting standards to ensure patient safety and product efficacy.
- Commercial Lighting: CNC metal spinning is also used to create decorative yet functional lighting fixtures, where aesthetic appeal is important. The process’s flexibility supports intricate designs that would be difficult to produce through other manufacturing methods.
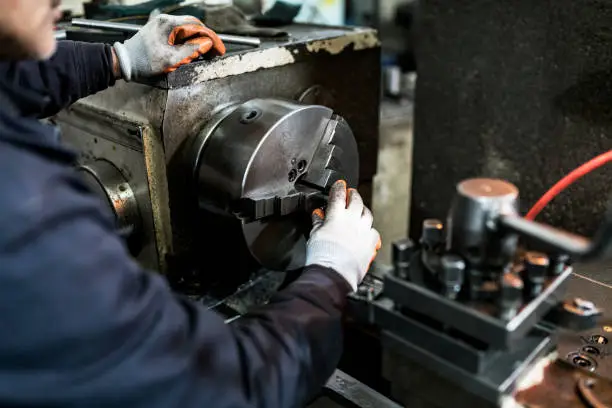
Future Innovations in CNC Metal Spinning
As technology continues to advance, CNC metal spinning is expected to benefit from several emerging trends that could enhance its capabilities further:
1. Integration of AI and Machine Learning: AI-driven analytics can optimise CNC programming by analysing large data sets from previous production runs, enabling predictive maintenance and identifying efficiency improvements. Machine learning algorithms could also enhance quality control by detecting minute deviations in real-time, ensuring consistent quality across all parts.
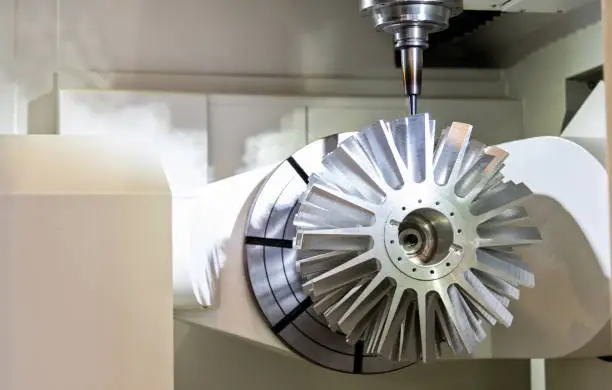
2. Simulation Software for Enhanced Precision: Simulation software allows manufacturers to model CNC spinning processes before actual production, identifying potential issues related to material flow, stress points, and deformation patterns. This pre-production modelling helps improve the quality of the final product by refining designs before any physical materials are used.
3. Hybrid CNC Spinning and Additive Manufacturing: Hybrid machines that combine CNC spinning with 3D printing capabilities are on the horizon, allowing for the creation of complex geometries that were previously unachievable. This integration would enable manufacturers to produce parts that require a combination of spinning and additive techniques, opening new possibilities in metal fabrication.
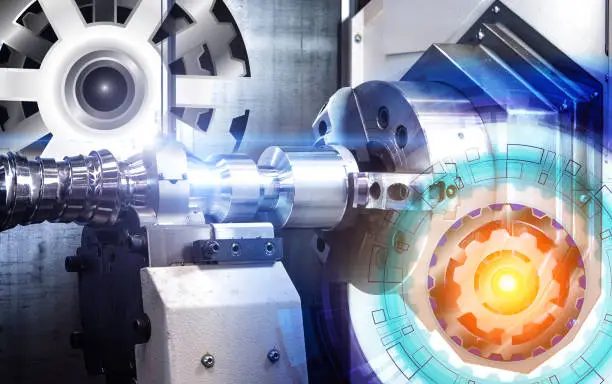
Advancing Precision and Possibilities in Metal Spinning
CNC metal spinning represents a powerful fusion of traditional metalworking and modern automation, offering unmatched precision, efficiency, and design flexibility. CNC metal spinning provides a reliable and cost-effective solution for industries that demand high-quality, complex components. As technology advances, the future of CNC metal spinning promises even more significant innovations, from AI-enhanced quality control to hybrid manufacturing methods that integrate CNC and additive technologies.
With its ability to produce parts with exact specifications, CNC metal spinning continues to set new standards in manufacturing, empowering companies to meet the challenges of modern production with confidence and precision.
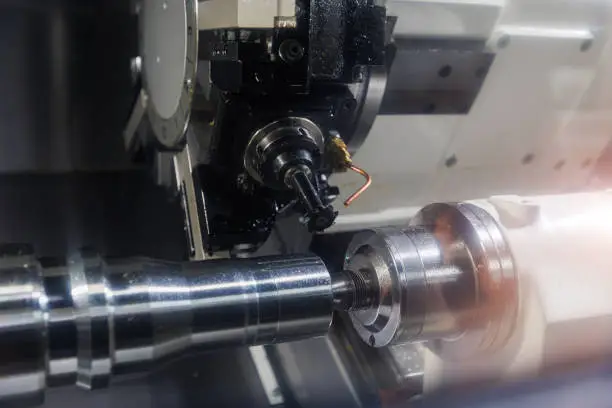
If you’re looking to leverage the benefits of CNC metal spinning for your next project, contact Tanfield Metal Spinners today. With our state-of-the-art CNC technology and commitment to quality, we’re here to deliver high-precision, durable components tailored to your needs. Contact our team to learn how we can support your manufacturing goals.